Audiovox Batch Builds (1/5)
Mar 9, 2016
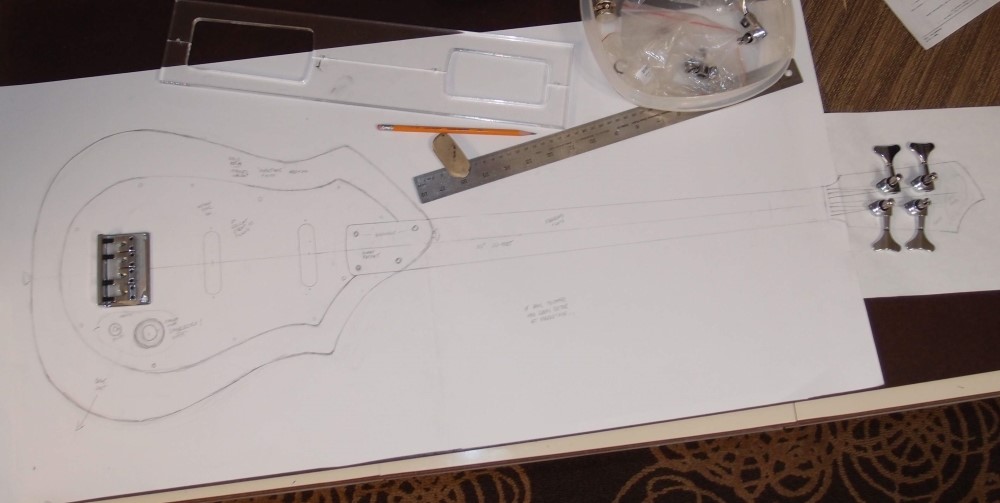
I have several of these necks and bodies roughed-out, and they feel much better than my first one, much better balanced. I knew that banjo neck would never play well, which is why I used a standard Fender profile on my first one. Banjos are made for picking. Intonation is one of those things where close is good enough, and with only 16 frets, I doubt it will ever be a problem. You'll be forever wiping smudges off that copper pickguard. I would shine it up and clear-coat it. Make a brass headstock tag and print out a waterslide decal to put on it. I posted the graphic above.
Mar 11, 2016
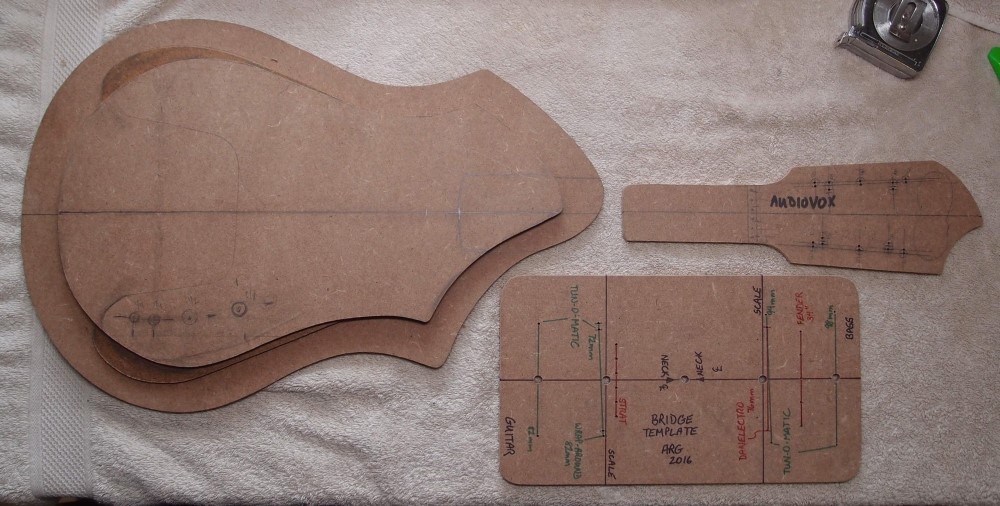
As I said, Tutmarc's design was less than optimal. It is almost impossible to arrange the headstock so all the tuners clear each other, the body is too small, the 'lap' curve is in the wrong place, and the whole thing is out of balance, sitting or standing. I know - I built one. You can see in these templates that I have addressed each of these issues, while maintaining the overall style of the original. I have a couple of bodies and one bass neck roughed-out, and when I clamp them together, they feel good. Like the body, the headstock maintains Tutmarc's reverse-flare style, but in a workable form.
Other changes are: a tone control, standard output jack, dual modern pickups, bass tuners, and a proper neck and bridge. This will turn out something like an old Vox Phantom or Teardrop, except that this shape actually works much better than either of those. This shape has very much normal guitar ergonomics, without bolting on all kinds of kludgy extensions like Steinberger had to resort to, to make his thing playable.
The Telecaster and Les Paul shapes were really nothing new, the breakthrough was Fender's extended upper horn, pioneered on the Precision and perfected on the Stratocaster. The upper horn allows much better balance on a strap. Without it, a normal 34" bass neck generally heads straight for the floor, so all of these will be short-scale basses or standard guitars.
The pickguard template is a modified tracing of the body of my first Tutmarc, which is fairly true to the original but slightly enlarged. The ass-end of the body template is roughly a Stratocaster, adapted to fit the poplar blanks I have which are a bit narrow. The chamber template is for hollow-bodies. The neck pocket is a standard Strat. The bridge template lays out all the common bridges for both bass and guitar, because I got sick of all the guesswork and fiddling. You can see the headstock is drilled for both guitar and bass, and the body allows for a range of bridge and pickup placements, so I can build pretty much any kind of instrument I want.
Poplar is a wonderful wood for a guitar body, think of it as 'eastern alder'. The necks will be standard rock maple. I've tried other woods for necks and found no reason to use anything else. These are woods I can easily source, there is nothing magic about walnut, Tutmarc used it for the same reason. Chambered and hollow bodies will use plywood sides and various faces.
This is an engineered approach to make this design work. In the coming months, I will have actual examples to show, but right now I have a ton of yard work to do. For the past month or so this project got shelved while I was building furniture - racks to store all these stupid things.
May 6, 2016
Box O 'Vox
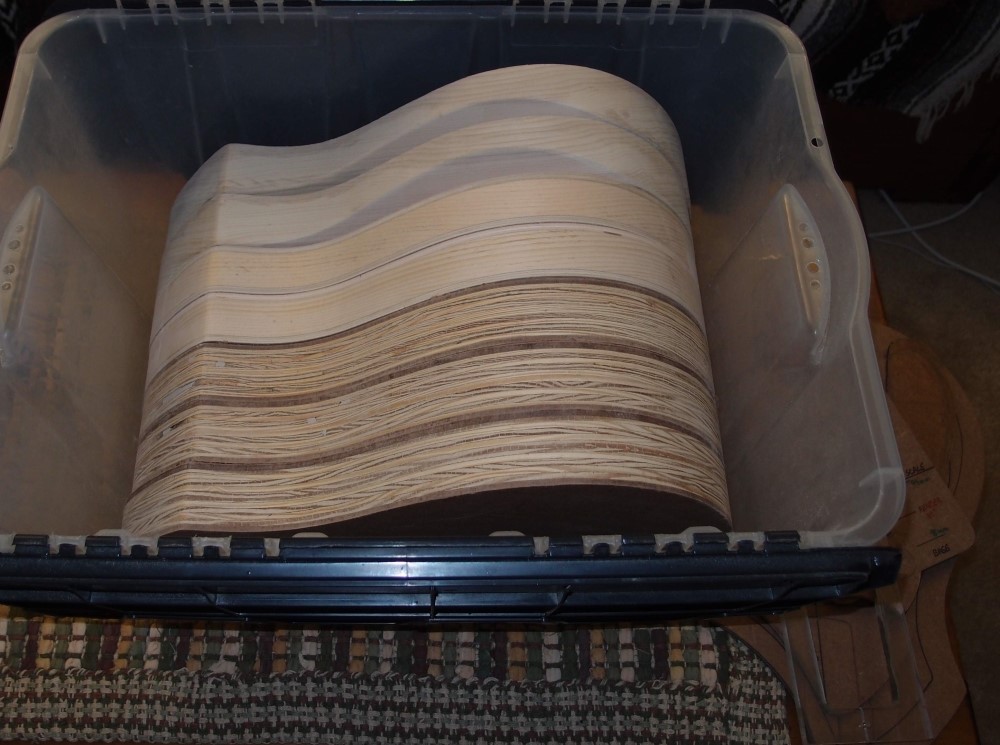
That's a whole lot of sawing and gluing and sanding. I need a shower and a nap.
Up to now, most of my builds were one-offs. I had a rough idea of what I wanted to make, but much of the details came during the build process - not the most efficient way to work. For these, I first made a full-scale drawing. From that I made a prototype neck and body, to make sure it felt good. From the prototype, I made the templates above. There are three templates for the body: the outside contour, the inside contour ( if hollow ) and the pickguard.
These are tracing templates, not routing templates. The actual shaping is done with saw and sander. Any time I can avoid routing, I do. As you can see, the bodies are all about as uniform as handwork will get.
The trick is the inside contour or cavity template for the hollow-bodies, which is most of them. The cavity, and the structure around it, are designed to allow for a wide variety of bridge, pickup, and control placements, given the size and shape of the pickguard, which is rather unusual compared to a Fender or Gibson. That also leaves a large block of wood at the ass-end of the body to act as a counterweight for the neck.
Thus, from one standard design, using a standardized neck pocket and cavity, I can build a guitar, or a short-scale bass of 20-24 frets, a baritone, or even a ukulele. I could also build a long-scale bass, but I have no interest in that, nor the two-octave short-scale, as the neck would be too long for the horn-less body, and the whole thing would be unbalanced.
This is very much the way Danelectro did things back in the day - one size fits all. I am still in awe of the wonderful and inexpensive guitars they built in the factory at Neptune. Too bad Paul Tutmarc didn't think like Nathan Daniel. I'm glad to see that someone has picked up the designs and tradition of Danelectro. Modern Danelectros are great guitars, well worth a look when you get tired of Fenders and Gibsons.
Back to the subject - it's going to be a long time before any of these are finished. I also have a box full of necks, and one bought one to study the scarf joint. Right now I just want to get all the gross woodworking done while I can set up outside and just let all the sawdust blow away and fertilize the grass. If not for the breather mask, I probably would have poisoned myself by now.
Two of the blanks are solid poplar, two are 5/4" soft pine from Lowes, which will be faced with nice hard maple plywood, and three are plywood from a dumpster, which will be faced with masonite - the greatest tone-wood of all! Damaged sheets of plywood and masonite can often be had at the hardware store for pennies, and are perfect for luthiery, but when I can trash-pick tone-woods, that's even better. 3/4" hard maple from Home Depot or Lowes is perfect for necks, the only thing that's harder to find is fingerboard material, except for more maple. Many flooring woods are entirely appropriate for fingerboards.
Nice day to do some gluing:
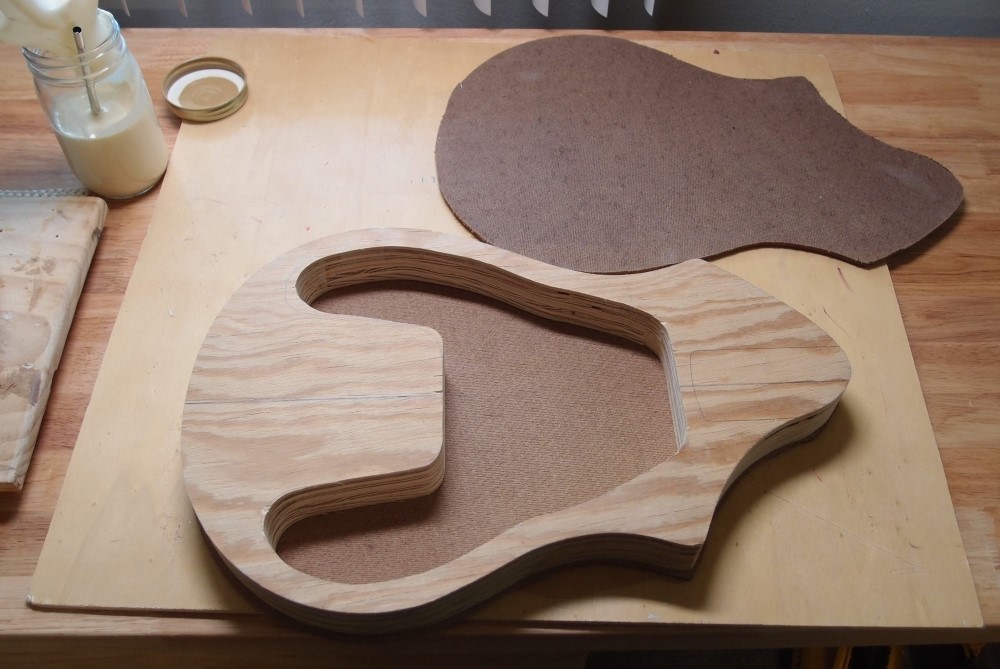
This is what the internal layout of the hollow-bodies looks like. It will never see the light of day again. The pine ones have thicker walls, as I have no doubts about the plywood, but the pine might crack if I make it too thin. The faces are oversized, so that they lap the entire edge of the frame. This is how the new Danelectros are made, the old ones used pieces of poplar tacked together to form the frame.
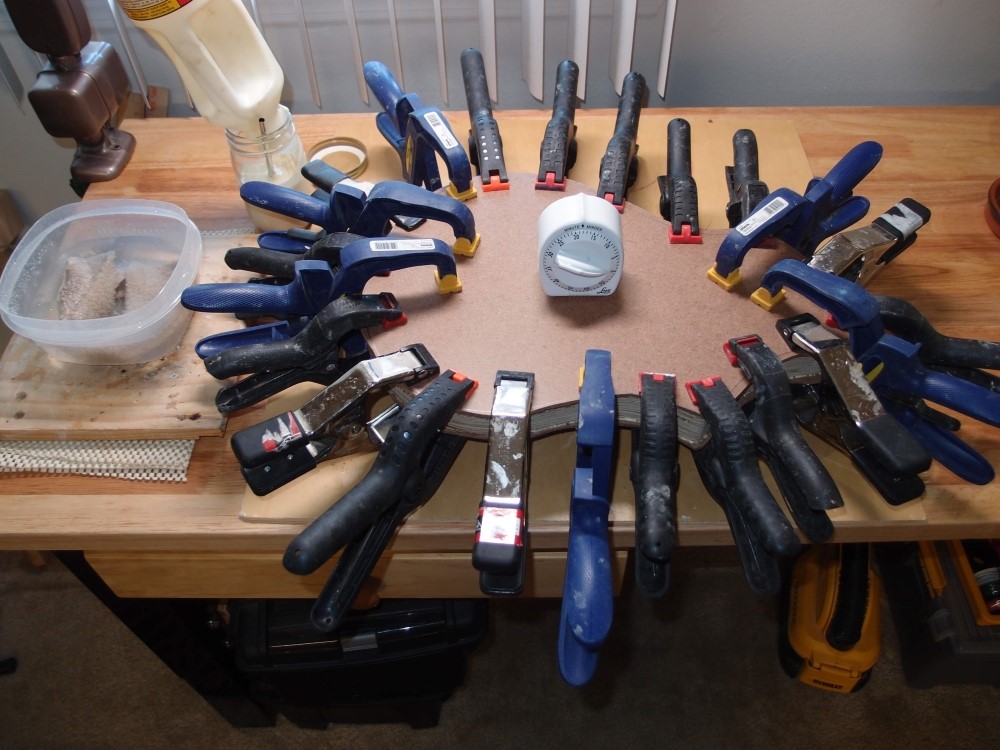
Bob Vila says you can't have too many clamps, and he's right. I don't have enough of these clamps to do more than one body at a time, so this is going to take a while. The little baking timer is a great help - I can go off and do other things while the glue sets up for 30 minutes, then come back and do another. A good day for gluing is cool and not too dry, so you have enough working time with the glue.
When they are all done, there will be one more trip to the belt sander to bring the rough edges in smooth. The plywood also needs some wood filler in spots. I like the two-part Minwax, which is just like Bondo. These Danelectro-style bodies will ultimately get Tolex bindings, so the finish on the sides doesn't matter much, but I don't want any holes. The masonite needs no sanding, filling, or smoothing at all, nor does it chip, you just have to be careful not to get it wet, and masonite dust is particularly awful. It's really a brilliant way to build an inexpensive but nice guitar.
Oh, the bell just rang ... back to it!
And finally, all edges filled and sanded smooth, and belly cuts on the solid-bodies. Using the templates, I can now lay out new centerlines, neck pockets, cutouts, etc. The solid and plywood bodies are 1-3/4" thick and weigh about 4.2 pounds. The pine bodies are 1-1/2" thick and much lighter at about 2.6 pounds. I don't want to hang a long heavy neck on a body that light, I will have to re-arrange my plans a bit. Time to build some necks.