Audiovox Batch Builds (5/5)
Mar 5, 2018
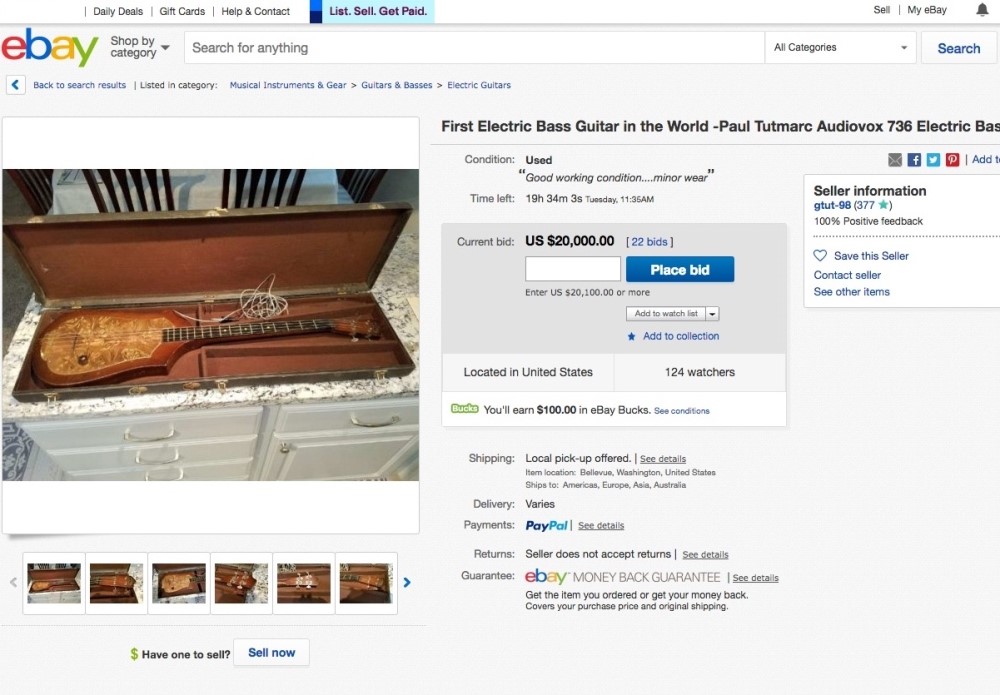
Somebody must be out of their mind. Bidding started at $1. It's a shame that a museum piece like this is going to be destroyed by FedEx. It would be safer screwed to the wall at a Hard Rock Cafe.
Mar 13, 2018

I finally finished this, on the right, next to the Uke bass. I don't even know what to call it. The starting point for the design is: capo a guitar at the seventh fret, and discard the highest and lowest strings. That leaves EADG like a bass, but up an octave from a standard guitar, with a 17-inch scale like a big ukulele. Then double all the strings like a mandolin, and what the heck, give it 24 frets. If anyone can come up with a workable portmanteau of guitar, bass, ukulele, and mandolin, I'd like to hear it. I know: guikulelin !!!
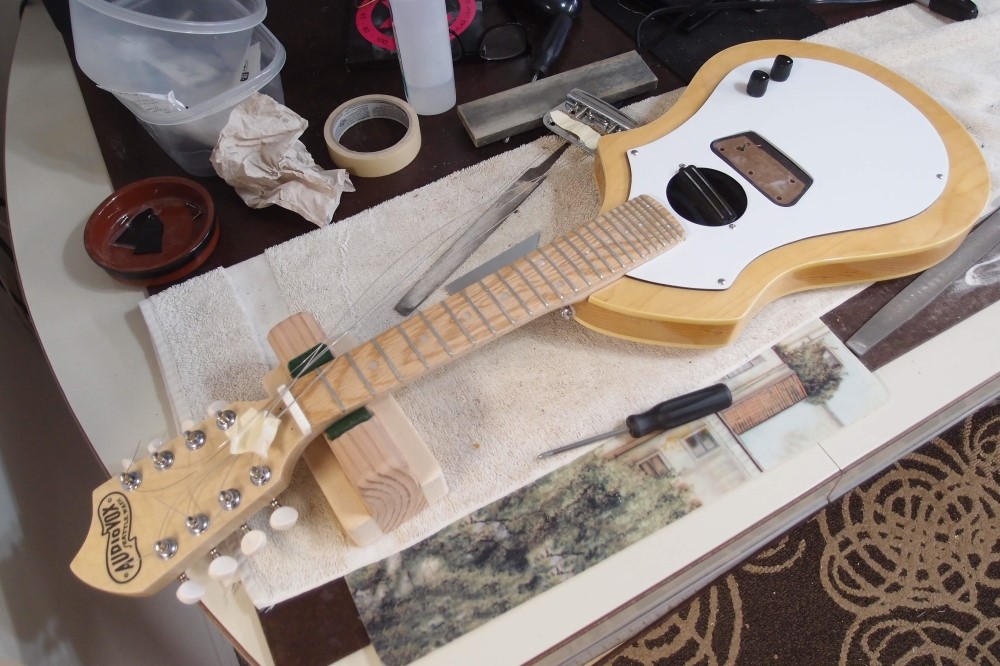
Here it is during its lengthy setup process. On its first assembly, I would rate it awful, but I made a list of all the adjustments and corrections, and tore it down, and fixed it. I had to rework the nut and raise the bridge up with a shim, as well as do a very fine fret leveling. I also fixed a brainfart in the electronics ( simple volume/tone, with a series/parallel switch on the tone. ) These Chinese tuners are the worst I've ever seen, but I tore them apart, lubed everything, and found the right place to smack them with a hammer, and now they are acceptable.
The build is very similar to the uke bass: 1" white pine core capped with maple plywood, maple neck with a red oak fretboard. This body is extremely light, probably too light to even carry a full-scale guitar neck, so this was a good way to salvage it. There are a lot of ugly modifications under the expansive pickguard, including a new bridge block where there was originally a pickup rout. The soundhole doesn't do much, but it adds a visual feature to what would otherwise be an awful lot of white pickguard.
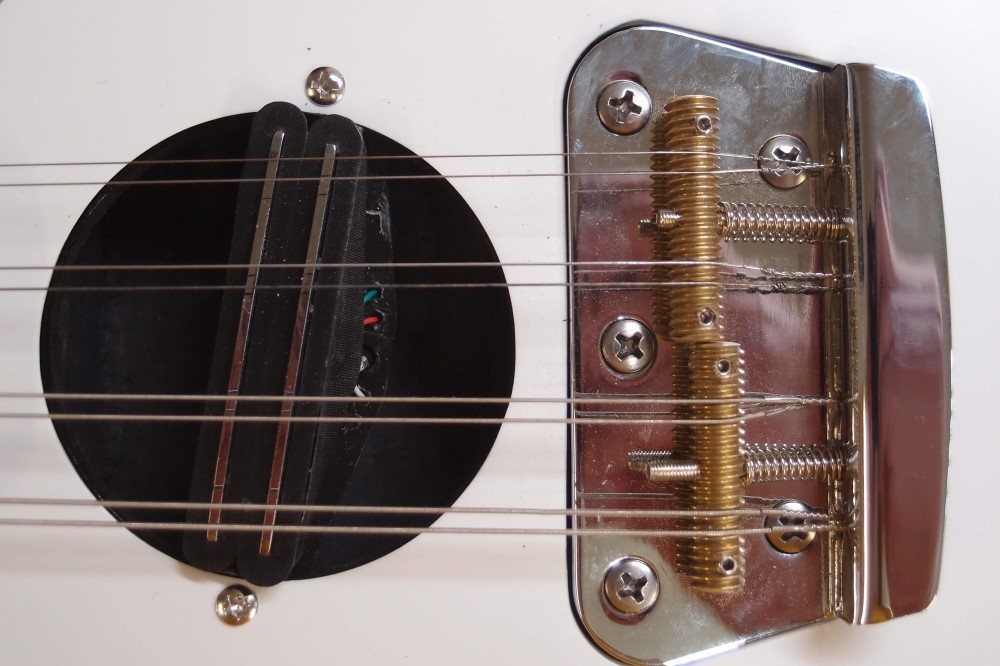
The bridge is a modified Bronco bass part. These are readily available and inexpensive, and have the advantage of being narrow gauge - the same string spread as a guitar. I made new saddles from 3/8" brass rod and spare parts. You could also use a 3/8" brass bolt from a marine supplies store, but I didn't think of that.
You can see the string spacing works out very nicely. I ended up shimming the bridge up with a piece of pickguard material, so I could have saved myself a lot of bother and just screwed the bridge down onto the pickguard without making a cutout, and then a shim to fill in the cutout.
The inter-string spacing is as a bass, and the neck is standard guitar width at the heel. A standard mandolin bridge is hooked for loop-end mandolin strings. I wanted to use regular guitar strings. I also didn't want a super-skinny mandolin neck.
The pickup is a cheap Chinese humbucker. I like these, they sound good for both guitar and bass, and there are 4 wires so you can separate the coils and do fun things. I like the soundhole mounting, and it is easier than making a tight pickup route.
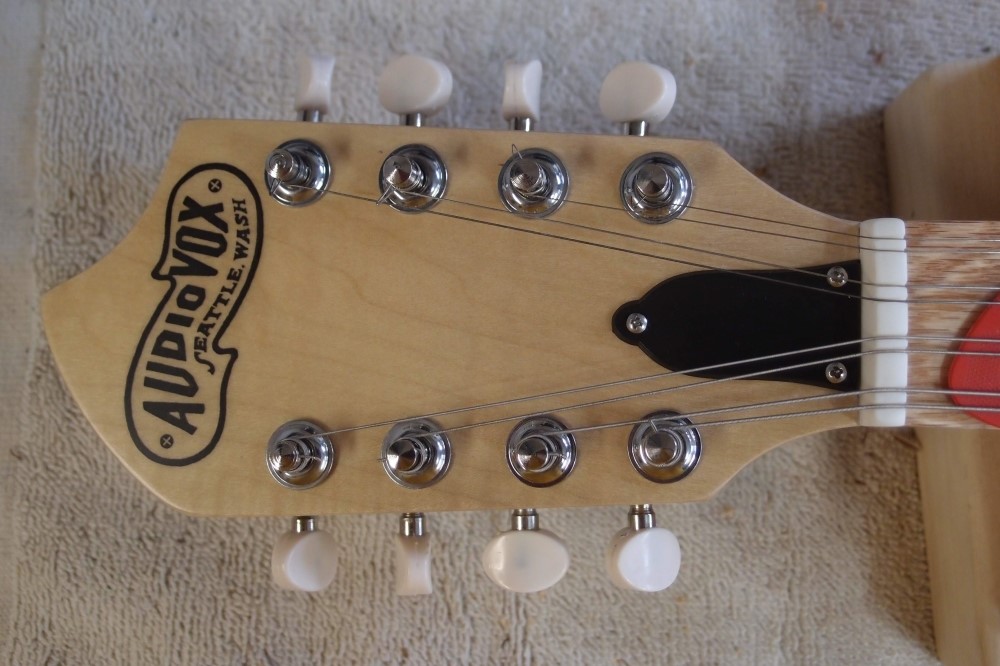
Here is a detail of the other end. The nut is bone, jazz-bass-width, and went through a good deal of production before I was happy with it. The truss rod cover is fake, there is no truss rod adjustment, just a steel bar. Another way to fill in otherwise empty space. The strings are all tuned in unison. I used 30-22-14-11, all from the big box of misfit strings. This is basically the middle four strings from a light guitar set, times two.
It sounds very dinky unplugged, but it sings when you plug it in. I'm kind of lost on a 17" scale, my fingers feel huge. ( A real mandolin has a 13" scale, I'd probably crush it. ) The frets above 20 are not very playable - just look at the spacing. You'd have to have some really hard callouses to make clear notes up there. But they look cool, and improve access to the frets that are playable, and lengthen a neck that would otherwise be even shorter. You can make power chords on the lower frets. An alternative would be to string it up DGBE, like the upper four strings of a guitar. Then you would have all of those chords instead. ( One of my goals was to build an instrument that didn't require a lot of transposing. I don't know a whole lot of guitar chords, and I'm damn well not giving up any. )
Jun 18, 2018
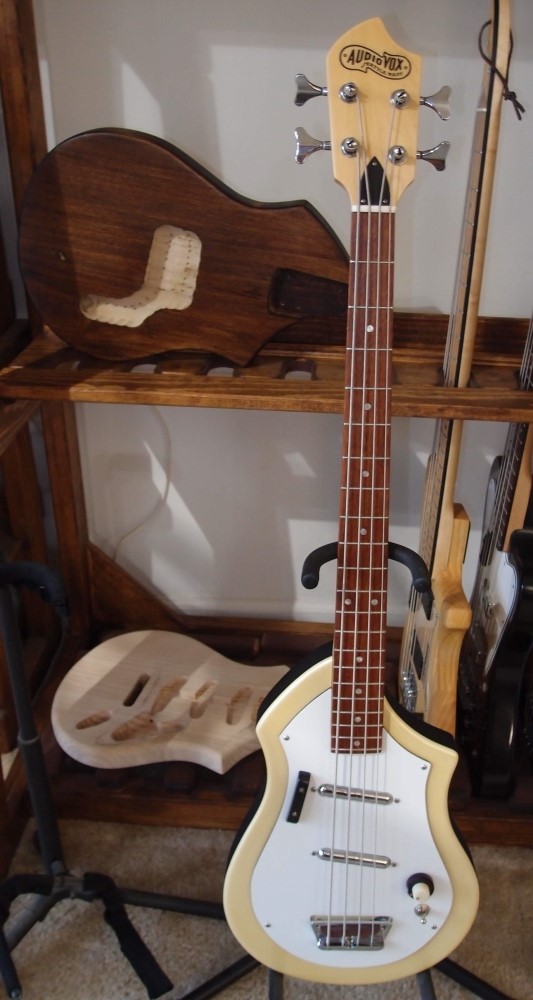
This is the last of the "main production run" that I started several years ago. This bass was intended to have a twin guitar, but that plan changed and the twin is not going to happen. This is pure Danelectro - pickups, controls, bridge, body. It plays surprisingly nicely, considering I just strung it up for the first time. After a few weeks, I will do a proper setup.
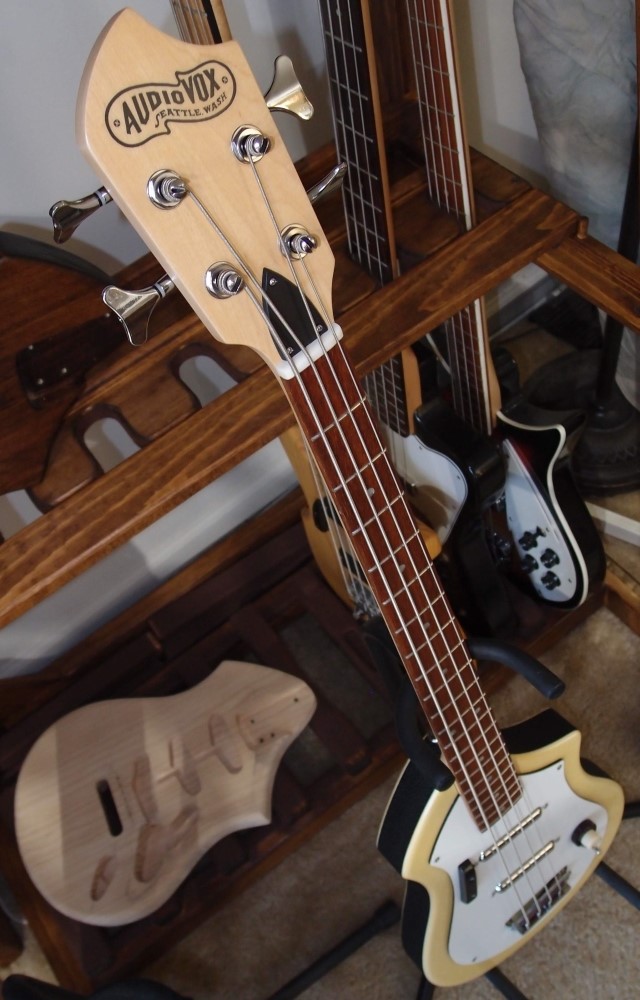
The fretboard is Brazilian Cherry, or Jatoba. Now that rosewood is all but illegal, this wood is going to become a major player. I expect very soon all the advertising agencies will seize upon its magical tonal properties, and the internet will become crowded with debates over whether it is lighter or darker. B*llsh*t. This wood is used a great deal as flooring and is readily available and relatively cheap. The hardness and grain are similar to rosewood, but it is not oily. On this piece, I applied two coats of real Tung oil. That darkened it considerably from orange to brown. Tung oil ( or linseed ) is a drying oil that is permanent, unlike stupid "lemon oil", which evaporates away after a few weeks.
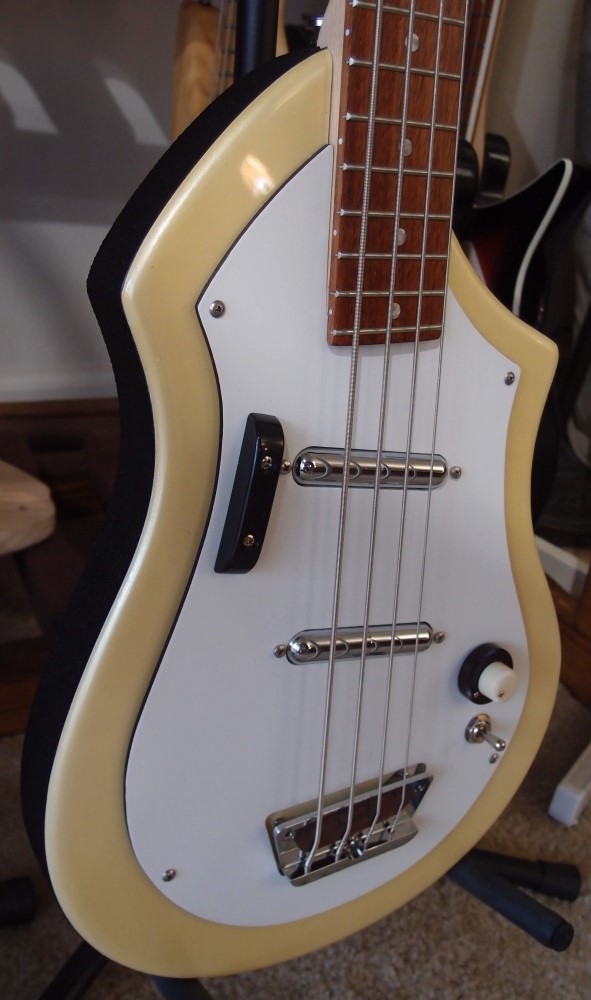
The precise cutout under the bridge. This way I can remove the pickguard without having to remove the bridge. The cutout was roughed-in with the scroll saw, then finished with files. The electronics are dead simple so that hopefully I will never need to remove the pickguard. The pickups are wired in series with a single Danelectro stacked control. The bridge ground is a piece of aluminum tape under the pickguard. I didn't bother shielding anything, lipsticks are pretty well shielded all by themselves.
I use a domed finishing washer under the back bridge screw, so I can cinch it down snug to the body. That is something Danelectro missed, it adds virtually nothing to the cost and makes the bridge mounting much better. The rest of the build is similar to my previous ones, 30" scale, double-acting truss rod, polyurethane finish ( pores fully choked! ) Home Depot maple neck, masonite over plywood chambered body. This is one of the first ones where I used wood glue to attach the binding after sanding the body edges down to bare wood. This is the only way that really works, and it is how Danelectro did it back in the sixties.
I love the sound of a Danelectro bass, which I attribute to the low-output lipstick pickups and rosewood bridge. The bridge intonates well enough. Intonation is more marketing hype than anything you can hear, especially under real playing conditions, close is good enough.
Aug 26, 2018
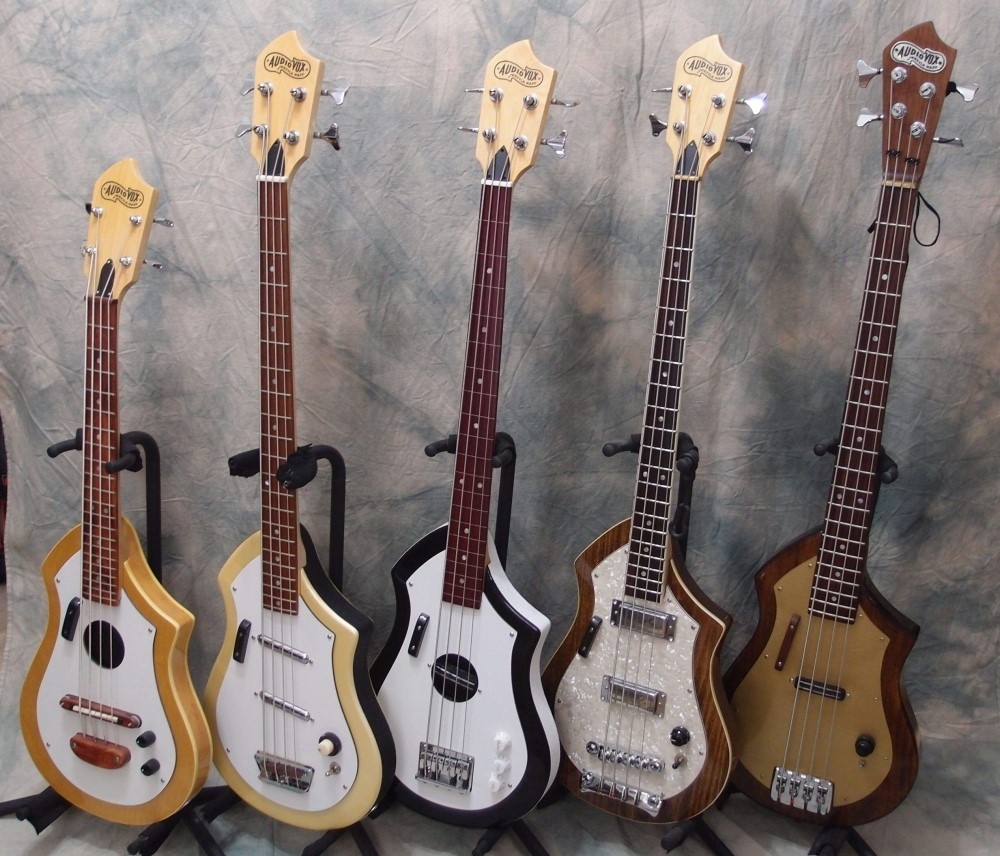
Here are all the basses together. Left to right:
- 21" hollowbody, plywood over pine
- 30" hollowbody, masonite over plywood
- 30" fretless hollowbody, masonite over plywood
- 30" solidbody, poplar
- 32" solidbody, poplar