August 18, 2020
Seeing Red
August 18, 2020
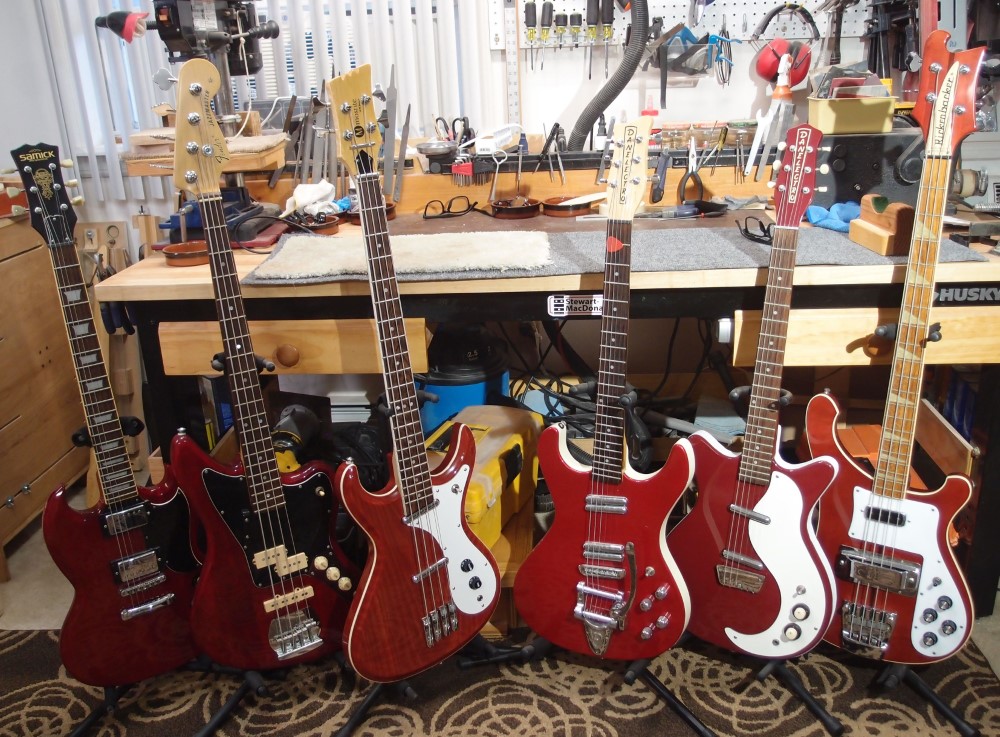
These all have one thing in common. What do you think that is?
Left to Right:
Samick SG
Samick makes a lot of Epiphone guitars, and probably a few Gibsons. This is an "Artist Express Edition" that they branded their own, and they pulled out all the stops. This is a really really nice guitar, and I got it cheap because it is a Samick. I'd say it is equivalent or even better than a top-of-the-line Epiphone. Needless to say, the quality is better than any real Gibson. When I got it, the fasteners were all corroded, so I replaced them with stainless from the local marina. I also replaced the knobs with nice silver-tops, and got a new switch plate. I gave the whole thing a good clean and polish and new strings, it really didn't need any setup. Korean quality is much better than Tennessee. Still not worth anything, but the nicest SG I've ever had my hands on. SGs are great fun little guitars, probably the best thing Gibson ever came up with.
This one has it's own entry in the website. I was so pleased with the first one, I decided to do a second. This is my first 32" conversion neck ( although not my first neck. ) It's not perfect, but it's good enough.
If you follow here, you've seen this one already.
Danelectro Hodad Guitar
This is a completely stock Danelectro Hodad from the 90s, made in Korea. These were all really great guitars. Danelectro went crazy on this one, with coil-tappable double lipsticks. To have that on a factory guitar back then was unheard-of. The Bigsby is really nice too. This one is in almost-perfect condition, even the binding. I traced it to make the Mosrite bass.
Danelectro DC-2 Guitar
Another one from the 90's, Korean. Back then they were making them a lot truer to the originals from the sixties. Note the knobs and classic rosewood bridge. This one is also in excellent condition, and I fixed the two typical problems with these: bridge collapse and peeling binding. The bridge plate is some sort of pot metal and sags in the middle over time. To fix that, simply place a small shim under the saddle to keep it straight. The binding job is covered in the Lab section.
Rickenbacker 4001 Bass
This is a 4001 from 1978 that I got in 1979. This is a rare all-red finish they called Burgundy-Glo. While many of these basses have neck problems owing to Rickenbacker's awful design, this one has always been straight and solid, even with round-wounds. A few years ago I replaced a lot of corroded parts with new real Ric parts, not cheap. That includes the tailpiece, tuners, and all the screws. You'd think for the kind of money these things cost, the tailpiece would be something better than pot metal, which had blistered up through the chrome. Likewise, all the nickel had turned black. Now it is all new. While I was at it, I added the 4003 tone switch, but wired upside-down, so that it becomes a 4003 when you pull the knob. I keep the strings slack on this one, because I don't want to tempt fate with the neck.