Working Metals
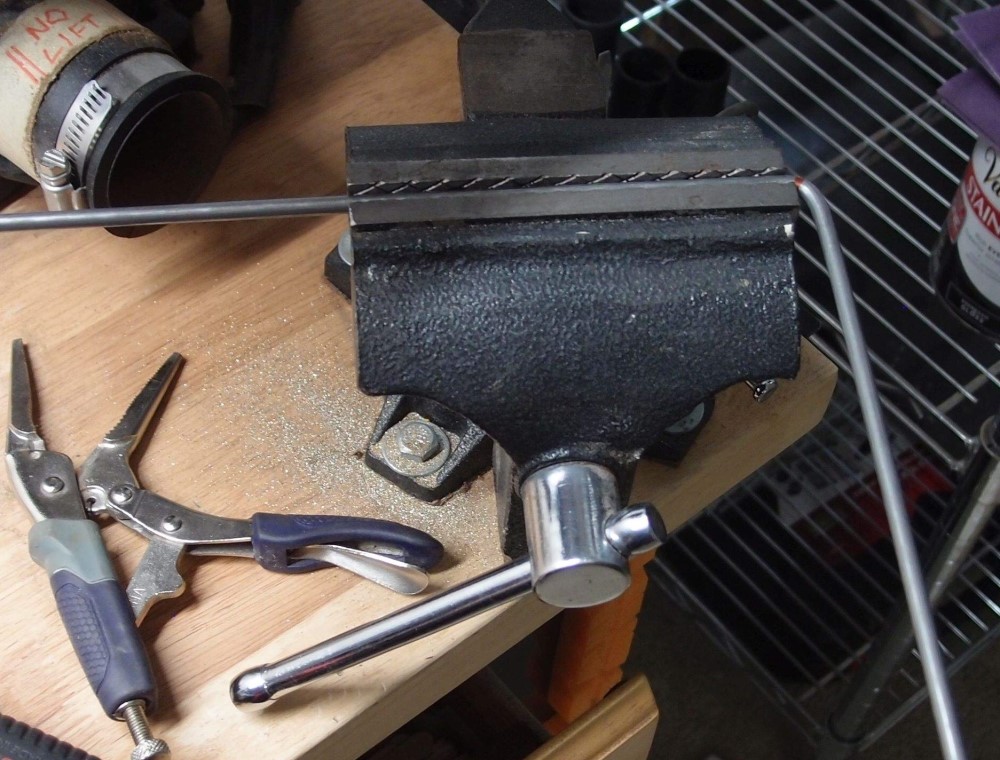
Bending steel is not that difficult. You can make a pretty tight bend up to 90 degrees in up to 1/8″ material simply by clamping it in a vise and hammering it over. To go beyond 90 degrees, say 180 degrees for a truss rod, first bend it to 90 degrees, then heat the elbow and finish the bend. Heat the bend point until it glows orange. For smaller (guitar-sized) materials, a common hand-held propane torch should be adequate. After bending, quench the part quick in water, like a blacksmith in a western movie. You can hold a small part under the faucet. That will restore the strength of the material.
Do not heat aluminum. Most of its strength and hardness come from heat-treating during manufacture, and the material will be effectively ruined if you take a torch to it, or even bake it. Aluminum doesn’t bend as well as steel, but I have bent 1/8″ aluminum up to 90 degrees the same way as I described for steel. At that point, you may start to see cracks, but unless your part is under a lot of stress, it should be alright.
The difficulty in bending anything thicker than sheet metal is estimating exactly where the final bend will be. Avoid this problem by doing the bend first, leaving the ends over-long and then trimming them to length. In cases where two or more bends need to be coordinated, get enough material to do a few test bends.
If you want to sound cool, don’t say “bend”, say “cold forge”.
Questions or Inquiries?
Just want to say Hello? Sign the .