Welding
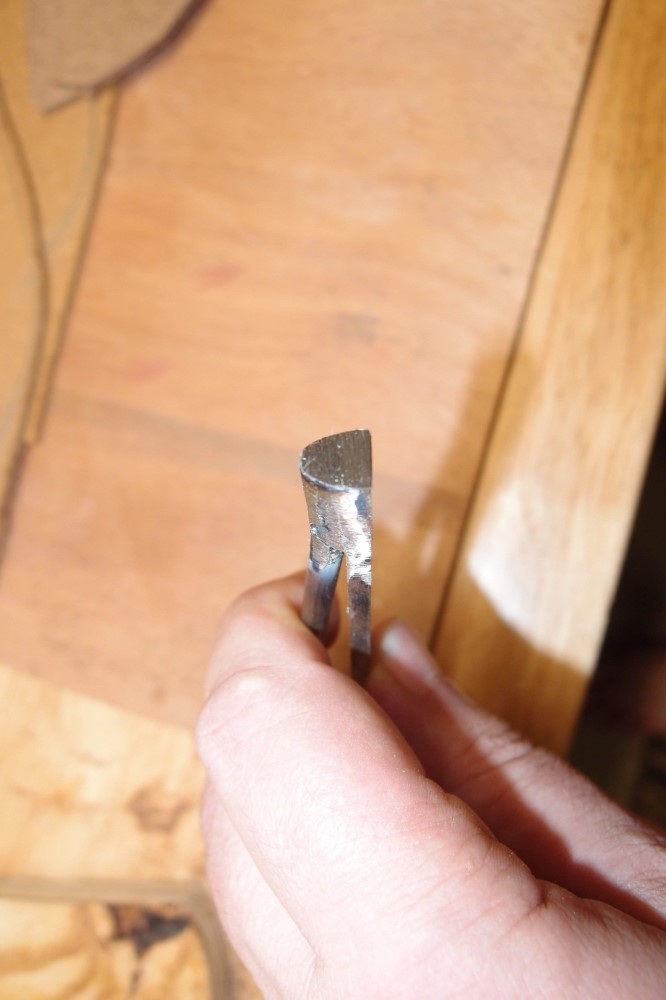
I was playing around with my new welder, and eventually, I did this. That is a 3/16" round attached to a 1/4" flat - a very common joint for a truss rod. It's not beautiful, but it is strong, you can see how I tried to pull it apart. Then I sawed the end off, and you can see it is solid - no slag inclusions, just two pinpricks at the 'corners' of the round. Welding is not as scary as I thought, but it is going to take a lot of practice. My welds seem to be a matter of luck, but my luck is improving.
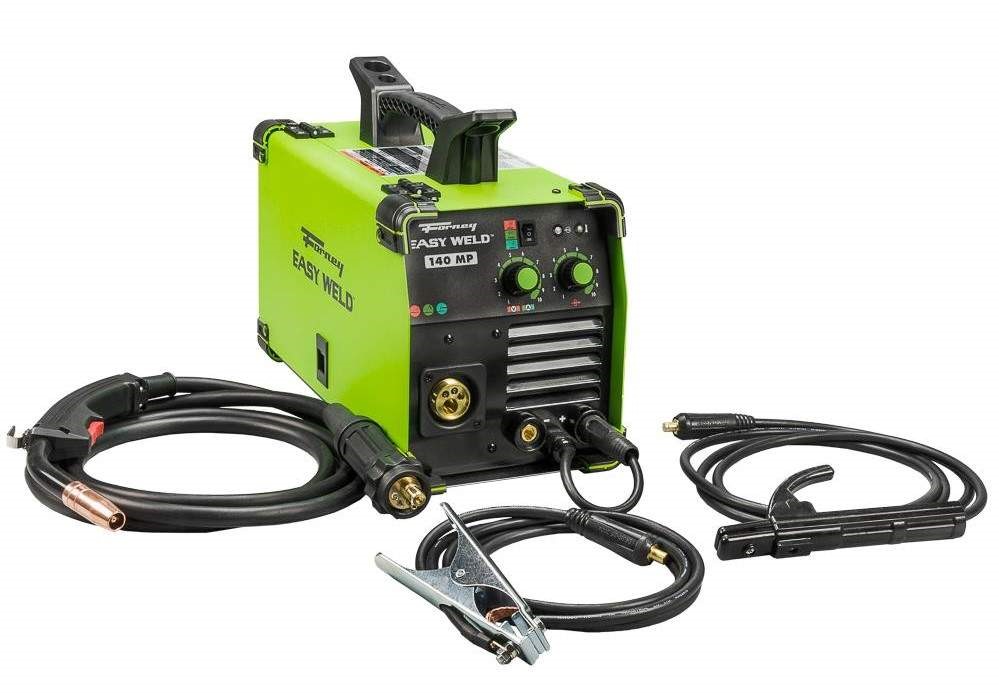
This welder will do four different processes: stick, MIG, gasless MIG, and TIG ( gun not included ). For now, I just have a roll of flux-cored gasless MIG wire, and learning how to do that well is challenging enough. I think that is probably all I will ever need.
The welder was free, but I needed a lot of equipment before I could use it - auto-dimming helmet, protection, consumables, etc, and I got a cheap little welding table from Harbor Freight, because welding on the wooden workbench didn't seem like a good idea. My next truss rod is going to be the most expensive one in history.
Unfortunately, the truss rod I was working on was ruined when the solder ran into the bearing. Maybe I could have torched it apart and cleaned it up, but I needed some test material for the welder anyway, so I sacrificed it. It's all cheap parts anyway; the most expensive part is the spoke nut, and that was not involved. With some decent metalwork solder and a propane torch, you can build your own truss rod with parts from Home Depot, and not have to depend on epoxy.
I just did some searching, and it turns out that cyanoacrylate and epoxy are roughly the same strength on most materials. Of course, there are many different kinds of epoxy. I had a feeling that Crazy Glue was comparable in strength to epoxy. For woodworking, Crazy Glue, epoxy, and regular wood glue all give a joint that is stronger than the wood, so except for boat-building, it makes little difference. I don't understand why people torment themselves with two-part epoxy when there are better easier cheaper alternatives. For me, it is a last resort. I've considered Crazy Glue-ing threads on a truss rod, but I never did it.
First Constructive Use of Welder
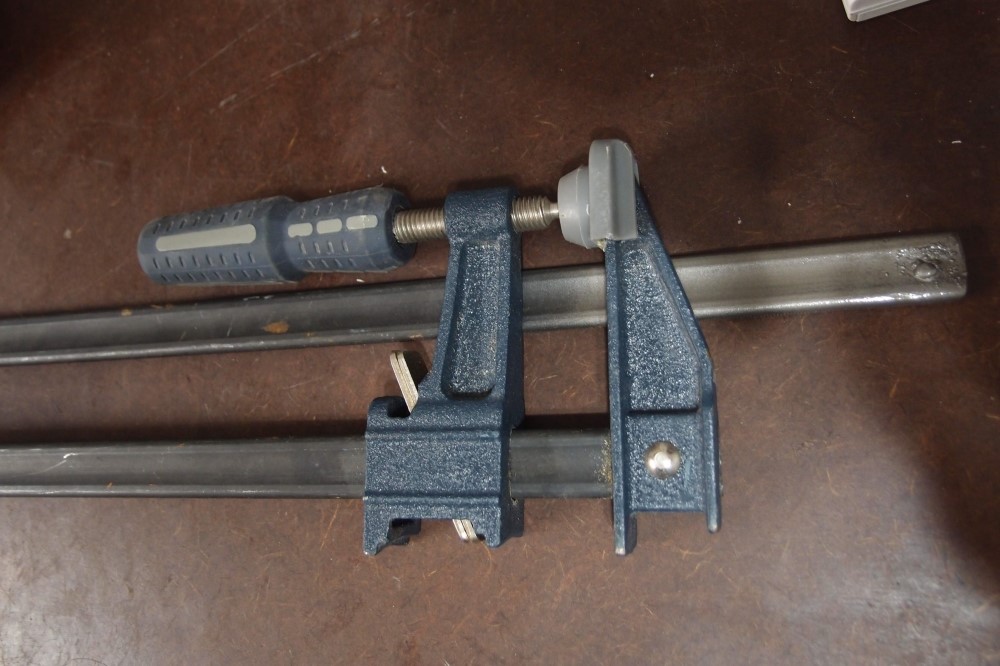
Up to now, all I have done with the welder is ruin perfectly good pieces of steel. It's going to take a lot of practice to get good with it. These are two Harbor Freight clamps, which I like for their light weight. However, at 36", these clamps are simply not stiff enough, they bend considerably under stress. Since I recently got some much better long clamps through the Home Depot Christmas every month program, I decided to cut these down to 18", and used the welder to make new buttons to keep the slider from going off the end of the bar. These clamps are perfect for gluing up Radiata bodies, and now I have four.
Questions or Inquiries?
Just want to say Hello? Sign the .