Stratocaster Uke Bass (2/2)
The new strings really pointed out the need for a proper piezo buffer, so I ripped out all the old electronics and rebuilt it. The one above is a different circuit that I did not use; I consider it a failure, but it was good experience building it. The guitar already had a battery box, and I decided to use a simple passive volume and tone control. A pull on the volume knob gives dead battery mode, and also allows comparison between buffered and un-buffered sound.
I made a new bone nut to replace the wooden one, and installed a chrome string hold-down. I found the bridge had bowed down slightly in the center under the increased tension of the new strings, so I inserted a piece of popsicle stick between the upper and lower halves, and then lowered it down as far as it would go. This bridge was designed for the silicone strings. The action with the new strings could still come down plenty, so I shimmed the neck back until it was nice and low. The action is very low and fast now.
Finally, I decided that since this was a major re-fit, I might as well make a new pickguard, in white to match the rest of my Strat-basterds. The new pickguard is a much tighter fit around the bridge, and as you see it in the picture, the intonation is spot-on. I left off the third control hole, with the option to drill it later. I had no black Strat knobs left, so I put on a pair of Jazz bass knobs from the junk box, and I like them, they can stay. So this one is not as slavishly dedicated to the Strat thing as the others. I like the clean and simple look of it.
I much prefer the sound of these strings to the old rubber-bands. The silicone strings are basically tone-less thumpers, these have much more character. The buffer allows the full range of the piezo to come through; without it, lows are noticeably attenuated. Much like the silicone strings, you cannot bend notes with these strings, nothing happens. They are also rather rough on the fingers - the round-wound coils are pretty large. Finally, they have no magnetic response, which is good, because otherwise I would have tortured myself installing another pickup and all the attendant wiring. Instead, I decided to go bone-simple ( although the powered buffer is one of the more complicated things I've ever assembled with a soldering iron. )
The amount of setup that went into installing these strings makes it a one-way trip - going back to the silicones is not an option now, at least not an easy one. But bad news: after fiddling with it a while, I find that the new strings are no good. They have a distinct underlying buzz, in tune with the note played. Nothing on the guitar is buzzing, it is the strings. It is audible both amplified and unplugged, so it is not just the brutal honesty of the piezo.
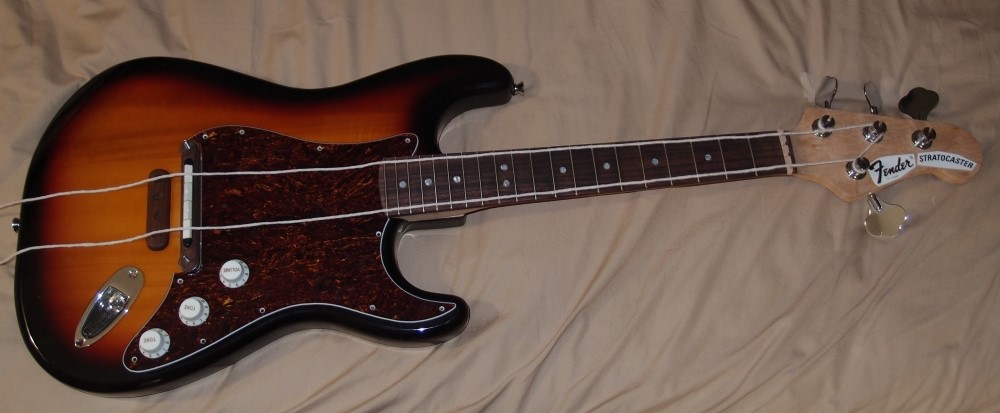
Update:
I think I figured out the problem. When I installed the sillycone strings, I rounded-over the bridge saddles to avoid cutting them. The new strings are extremely sensitive to the break-over angles at the nut and saddles. The buzz was largely coming from the bridge saddles, much like a sitar, and was worst with the largest string. I filed the saddles back to a sharper edge, and the problem has largely gone away. There is still a problem with the break-over angle of the G at the nut - I will have to come up with some sort of hold-down there.
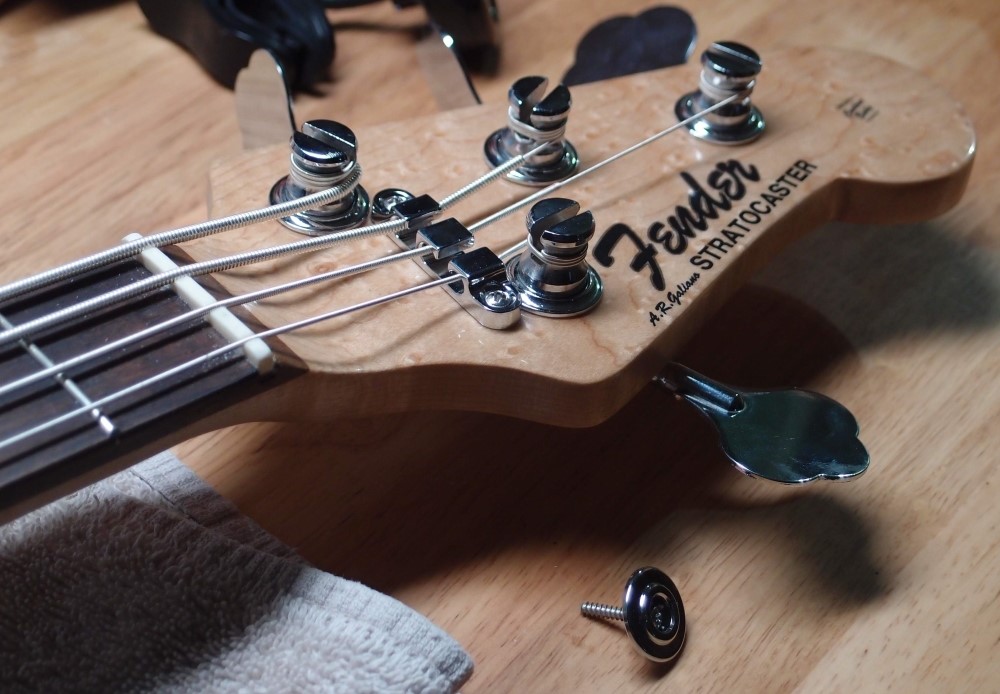
Here is the solution to the nut-end problem. These are made by HipShot. I got it on eBay. There are a number of different models and finishes. Much better than the standard round string retainer. It even covered up the old screw hole.
I just finished rewiring the "Stratbory" . That's a 21.5" scale, rubber-band strings with a piezo saddle in an adjustable floating bridge, and a carved walnut tailpiece. Semi-active electronics, with bass boost and treble cut. The nut is maple, and the E and A tuners are drilled out for those super-fat strings. Look close - the custom neck is birdseye. Total cost: $170, now that the expensive electronics are out of it.
A few notes on this type of instrument:
The strings are fairly fragile, especially the thinner ones. Anything that touches them has been carefully radiused and smoothed to avoid damaging them. That includes the bridge saddles, which have rounded notches filed into them. The tailpiece protrudes from the body to lessen the break-over angle at the bridge, while hiding the unsightly string knots inside the body. A pretty clever use for the tremolo hole, I think.
Surprisingly, the fatter strings are actually fairly stable in tuning, even in the long run. Alas, the same is not true for the thinner ones. As for longevity, that test is ongoing, but there is already some 'necking' present. New strings stretch like crazy and take at least a week of retuning to achieve even short-term stability. You have to get the length of those big fat strings just right, because you can't wrap much excess on the posts. I ended up shortening them several times before the tuning stabilized.
The original Ashbory design is an unmarked fretless 18" scale. Good luck playing that in tune - every error in finger placement is going to be magnified two-times compared to a 36" bass. That's why mine is fretted, for 'precision'. I stretched the scale a bit for easier fingering, but I do not consider anything above the octave really playable. A guitarist who is used to the crowding up there might find it more acceptable.
The strings are too sticky to do much sliding on, and bending is pointless - nothing happens, and they tend to roll when you push then sideways. The instrument is also fairly insensitive to intonation; although the floating bridge is fully adjustable, it doesn't seem to make much difference. The action is higher than usual for metal strings; at least the rubber bands don't buzz. You can slap and pluck it, but the thumb slap doesn't sound so good, and the finger pluck is just asking for a broken string, so I don't do it.
The sound is somewhat like a double bass. I suppose, if you have that in mind already, you will make yourself hear it. ( "Tone" is at least 50% imagination and expectation. I don't even like the word. For cork-sniffers, 90% is a better estimate. ) Mostly, it has its own sound, kind of dull and thuddy to tell the truth. As I said, too much treble results in annoying finger noise, so you want to keep the tone down deep.
The piezo pickup senses all the higher harmonics without filtering like a magnetic pickup. This results in a much more acoustic sound. The response is excellent, which I credit to the solid integration with the saddle and supporting structure, and a good break-over angle from the bridge to the tailpiece. I have a spare one of these pickups, it would be interesting to build something similar to this but longer scale with metal strings.
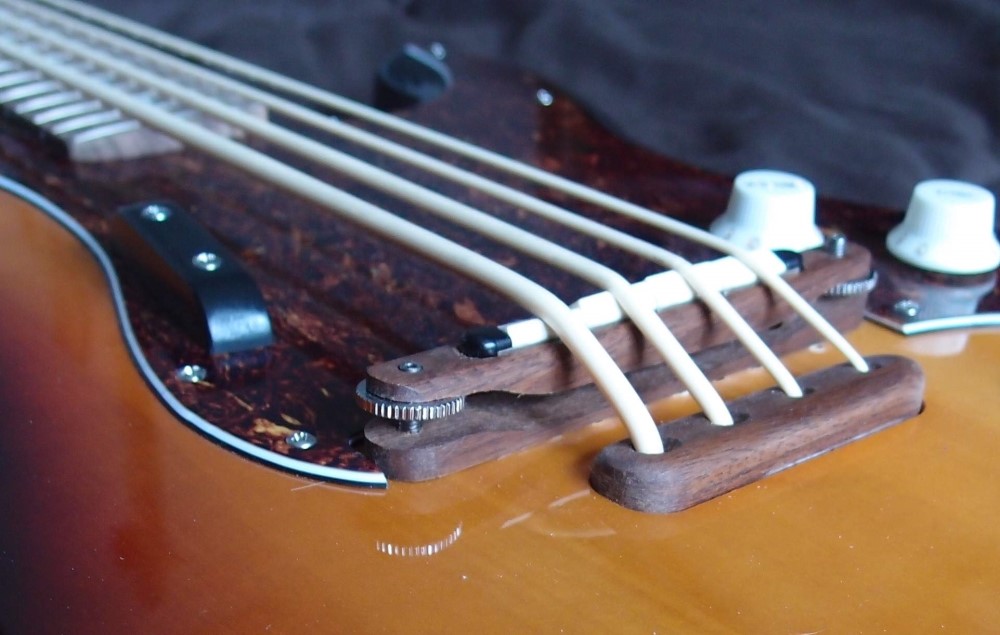
The saddle is a Washburn piezo, with individual compensated saddles, although I think there is just one big piezo element underneath. It is for one of their acoustic basses, I think, or it might not even be a Washburn at all, I'm not certain. I blunted the saddles a bit so they don't cut the rubber strings.
The bridge is milled from 2 pieces of walnut scrap. The upper piece is slotted to hold the saddle, the lower piece rests on the body with thumb screws between to adjust for height. So it is a floating design - you can adjust for overall intonation by moving the entire bridge. It is like a Hofner bridge, or a Jazz-box guitar, except made to hold the piezo.
It is as low-profile as I could make it, because the flat neck installation on a Fender doesn't allow for much bridge height. It took a couple of tries to work out the right order of operations. Mill the slot first into a large blank, then mill the bridge down around the slot. I say mill, but it is actually a combination of router, drill press, and belt sander.
Walnut is nice strong wood for this, and resembles rosewood. If I didn't have the walnut lying around, I would have used maple. Doesn't make any difference, as long as it is strong enough not to sag over time. Oak would probably work, poplar or pine would be a bad choice. Of course, rosewood is much harder and stiffer, but you don't need that much overkill.
If I remember correctly, and it certainly looks that way, no intonation adjustment was needed with the rubber strings, in fact, they hardly respond to any if you try. So the compensated saddles are doing nothing, but the part works and sounds excellent; I even got a second one to mess with someday. Again, this relates to the stiffness of the strings, and these have practically no stiffness at all, hence need no compensation. Just put the bridge at the scale length, and you're done.
As I and others have pointed out, you also can't bend notes on one of these - they simply do not respond to small changes in tension. Tuning them up is an interesting exercise - crank and crank and crank, but you don't want to do it too fast, or you'll wreck them. Eventually they become stable. I ordered a set of the new nylon-core metal-wound strings to put on it in place of the rubber ones, because I just don't like them. I'll post an update, but I don't know when that will be, as they are on back-order until forever.
I went to all this trouble because I had no idea what to expect with the rubber strings, so I allowed for everything, and I'm glad I did. Right now the bridge is tucked up against the pickguard, but I'm sure with the metal strings I will end up adjusting it back. Or maybe not, I don't know, and there isn't a lot of information you can find about these things. I can set the intonation of a set of roundwound 105-50s with a yardstick and it sounds just fine, but this is terra incognita.
The tailpiece is another scrap of walnut, fitted into the tremolo hole, backed with a piece of plywood. It is held in by the strings alone. The tremolo hole is offset to one side, so the neck is mounted slightly crooked in order to be straight. And while I'm at it, here is the headstock:
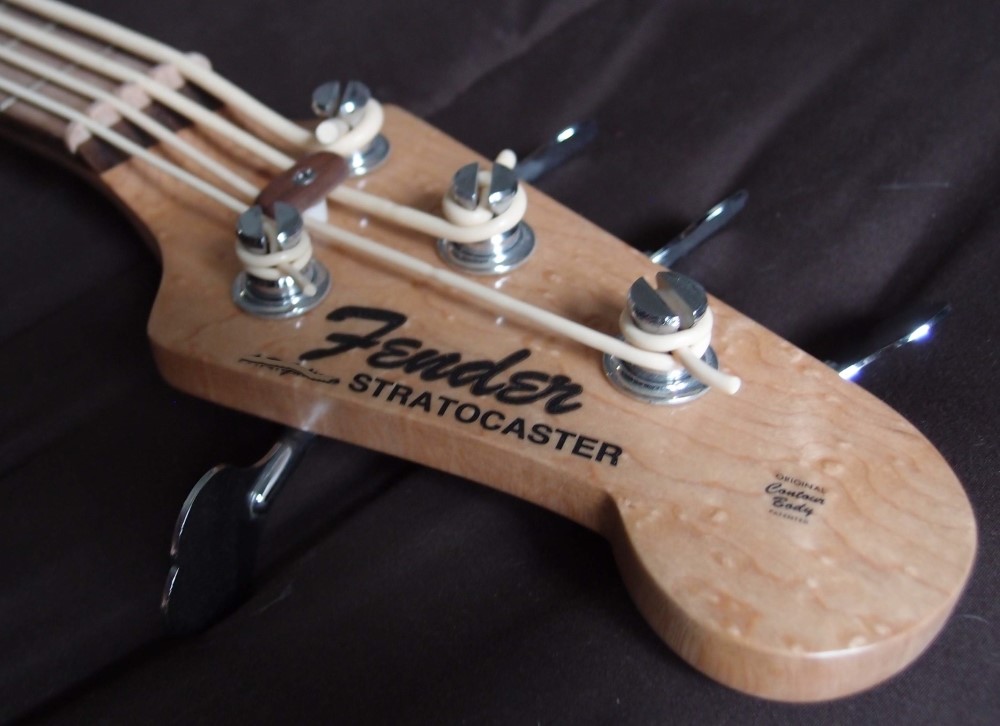
The nut is maple. The E and A tuners are bored-out to accept the fat strings. The Musicman style tuner layout avoids too long a run to the G tuner, because I wasn't sure if the strings would be long enough. The birdseye is Home Depot, and the trussrod is a piece of 1/2" steel square tube - the actuator linkage from a broken recliner that I fixed. I hope the decal isn't fooling anybody. It was a fun build.
Note: When I replaced the rubber-band strings with metal ones, I replaced the nut with a more conventional one.
I finally assembled all the parts. I've had the body and neck hanging around (literally) for a long time. I had the bridge design already, but wasn't sure what to do for the tailpiece. Finally, I dreamed up what you see.
The nut, bridge, and tailpiece are all made from scraps of the fretboard wood. It was sold to me as Bubinga, but I doubt it. In fact, the piece was so ugly that I complained and got a refund. Later, I cut around the worst of it for this ultra-short fretboard, which left lots of scrap. I coated the nut with Crazy Glue for reinforcement. The bridge and tailpiece are glue-ups of the 1/4" fretboard stock, shaped on the belt sander.
The body is maple plywood over a 1" pine core; the sound hole is real ( looks painted-on. ) The sound hole doesn't do anything except visually fill up the big blank space. The pickguard is white-painted masonite, as cheap as you can get. I wrapped a vegetable can in sandpaper and whirled it in the hole to get it perfectly round. I painted the interior of the body flat black to make the sound hole pop visually.
The 21.5" neck is Home Depot maple, with a steel tube truss rod to prevent it from ever warping. The truss rod cover is just for looks. It uses four 'economy' guitar tuners; I left the covers off for an old-timey open-gear look.
For electronics, there is a piezo saddle and one of my home-made one-transistor impedance buffers, into passive volume and tone. I fooled around, and decided to go with a 'B' pot for volume and an 'A' pot for tone. A pull on the volume disables the buffer and lets you hear just how bad an unbuffered piezo sounds. Getting at the electronics is a lot of work - you have to remove the tailpiece to get the pickguard off.
The strings are U-Bass Silver plate round-wound. If not for these strings, I would never have built another uke bass. In fact, I would have taken apart my Strat-uke-bass and re-used the body for something else. I just can't stand the regular rubber uke bass strings. These feel and sound more like normal bass strings. The sizes are .050-.065-.095-.110, almost like regular strings. You lose the double-bass sound, but they are much more playable. These strings use a non-magnetic metal winding around a nylon core. They are relatively insensitive to bending and intonation, and more prone to rolling under your fingers than metal strings. The nylon core is going to take several weeks to stretch and stabilize, until then it is constant re-tuning. The entire set went a half-step flat overnight.
These strings probably have about the same tension as nylon classical guitar strings, so you can get away with a lot in terms of securing them. Bass tuners are complete overkill, and the two screws securing the tailpiece are more than enough. My only worry is that the bridge may sag over time. My original was made of walnut, which proved to be not strong enough. Whatever this wood is, it is much stronger than walnut. In fact, I started making a replacement bridge for the that one.
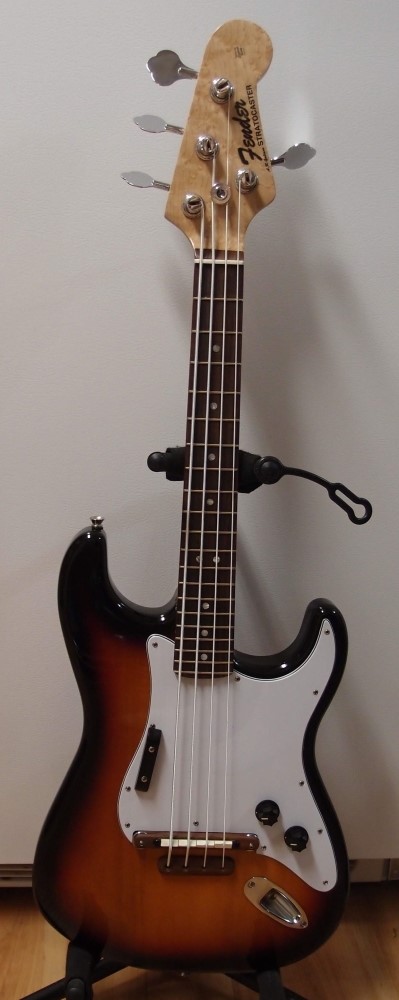
After I re-strung this little guy with the new Kala U-Bass metal-wound nylon core strings, I found it needed some modifications to perform at its best. To re-cap, this is a 21.5" scale custom neck on a Stratocaster body, with a piezo-loaded floating bridge. The tailpiece is actually in the tremolo hole, with the neck realigned to match.
The new strings really pointed out the need for a proper piezo buffer, so I ripped out all the old electronics and rebuilt it. The guitar already had a battery box, and I decided to use a simple passive volume and tone control. A pull on the volume knob gives dead battery mode, and also allows comparison between buffered and un-buffered sound.
I made a new bone nut to replace the wooden one, and installed a chrome string hold-down. I found the bridge had bowed down slightly in the center under the increased tension of the new strings, so I inserted a piece of popsicle stick between the upper and lower halves, and then lowered it down as far as it would go. This bridge was designed for the silicone strings. The action with the new strings could still come down plenty, so I shimmed the neck back until it was nice and low. The action is very low and fast now.
Finally, I decided that since this was a major re-fit, I might as well make a new pickguard, in white to match the rest of my Strat-basterds. The new pickguard is a much tighter fit around the bridge, and as you see it in the picture, the intonation is spot-on. I left off the third control hole, with the option to drill it later. I had no black Strat knobs left, so I put on a pair of Jazz bass knobs from the junk box, and I like them, they can stay. So this one is not as slavishly dedicated to the Strat thing as the others. I like the clean and simple look of it.
I much prefer the sound of these strings to the old rubber-bands. The silicone strings are basically tone-less thumpers, these have much more character. The buffer allows the full range of the piezo to come through; without it, lows are noticeably attenuated. Much like the silicone strings, you cannot bend notes with these strings, nothing happens. They are also rather rough on the fingers - the round-wound coils are pretty large. Finally, they have no magnetic response, which is good, because otherwise I would have tortured myself installing another pickup and all the attendant wiring. Instead, I decided to go bone-simple ( although the powered buffer is one of the more complicated things I've ever assembled with a soldering iron. )
The amount of setup that went into installing these strings makes it a one-way trip - going back to the silicones is not an option now, at least not an easy one. But bad news: after fiddling with it a while, I find that the new strings are no good. They have a distinct underlying buzz, in tune with the note played. Nothing on the guitar is buzzing, it is the strings. It is audible both amplified and unplugged, so it is not just the brutal honesty of the piezo.
Update:
I think I figured out the problem. When I installed the sillycone strings, I rounded-over the bridge saddles to avoid cutting them. The new strings are extremely sensitive to the break-over angles at the nut and saddles. The buzz was largely coming from the bridge saddles, much like a sitar, and was worst with the largest string. I filed the saddles back to a sharper edge, and the problem has largely gone away. There is still a problem with the break-over angle of the G at the nut - I will have to come up with some sort of hold-down there.
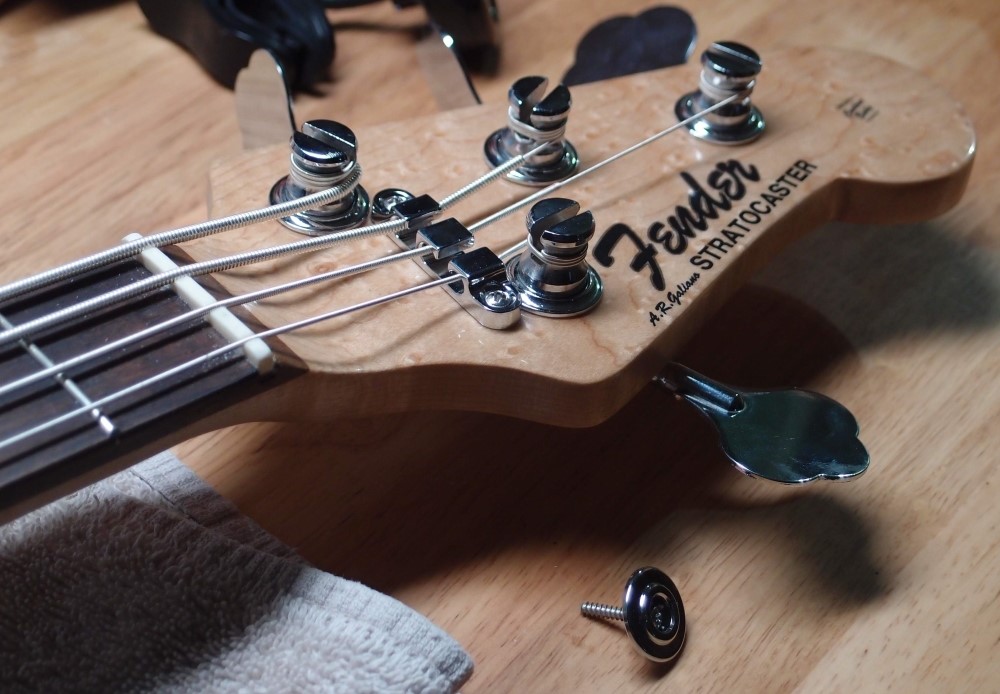
Here is the solution to the nut-end problem. These are made by HipShot. I got it on eBay. There are a number of different models and finishes. Much better than the standard round string retainer. It even covered up the old screw hole.
Questions or Inquiries?
Just want to say Hello? Sign the .