Neck Mountings
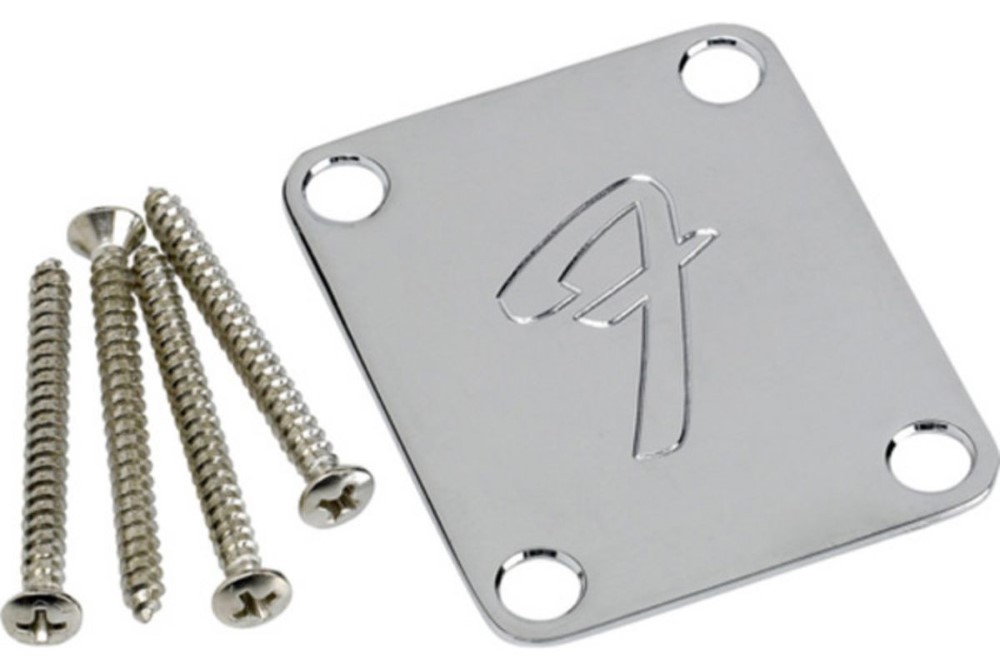
There is a lot of nonsense that gets floated through the guitar industry about neck mountings, mostly invented by marketing departments to justify outlandish prices. 'Set' and 'through' necks are simply luthiery baggage from the middle ages, literally, as in 500 years ago before screws had been invented, or at least were in common use. Any difference in tone or sustain is purely imaginary on the part of the sucker who paid an extra thousand dollars for it, and has no choice but to believe the BS or admit he was had.
I'm not saying non-bolt-on joints can't be made to work, and work well if done properly ( as in not the way Gibson does it ) but they are neither necessary nor superior. Here is a stunning picture of how Gibson does set necks:
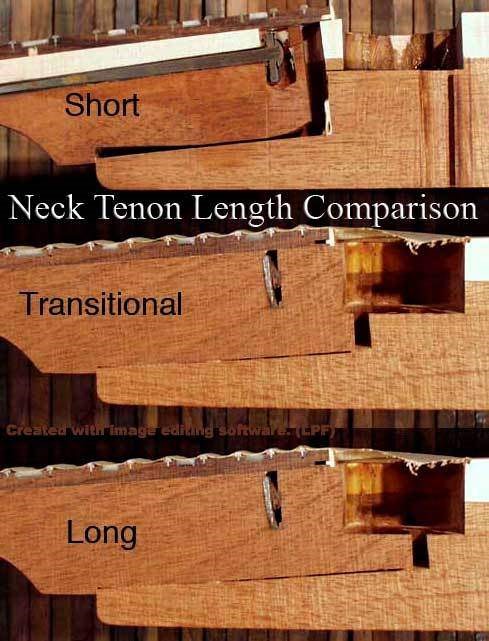
Needless to say, the bulk of their production is 'short', only the most expensive models get the better neck joints. The short joint is just floating in there, practically no contact area. If the neck joint really has any effect on sustain, why do they make these, and how on earth do they sell them? Maybe if they put a thin lacquer finish on it so the wood can breathe ...
Even for the better Gibson joints, cutting those angles just right is a real bother, and even with factory fixturing, you're going to end up with a certain reject rate when the glue has dried. And look how thin the body is under the neck. What is stronger about that?
From an engineering point of view, the neck joint merely needs to be strong enough, that is, stiff enough not to damp the vibration of the strings, or shift and affect tuning. For centuries, strong enough was achieved with primitive animal-based (hide) glues on whatever kind of wood was available, along with careful fitting of handmade joints. That degree of strength can easily be exceeded with steel screws set into hard maple with a steel backing plate. The fact that such a joint is adjustable is a huge bonus, as well as the fact that the parts can be replaced individually if they fail. Even the Gibson 'short joint' above, awful as it looks, must be strong enough or they wouldn't be able to sell it.
As long as any neck joint is 'strong enough', they are all equally good in terms of tuning, tone, and sustain, meaning that they have no effect, positive or negative, on anything at all. Only a bad neck joint can have a noticeable effect, and that will always be negative, and probably never get out the factory door.
The only major downside of the bolt-on neck is the bigger neck heel, which some people complain about, although many ( like Eric Clapton and Geddy Lee ) seem to have no problem with. Note that it is also possible to extend the neck heel beyond the fretboard into the body and still use a bolt-on adjustable attachment. The only guitar I know of that is built this way is Brian May's original Red Special, although I don't know if it is actually adjustable. Rickenbacker also uses an extended neck heel, but they glue it in.
And of course on my trusty old 4001, the neck runs clean through the body, which is really neat until it warps some day, then the whole thing will be trash. I love my old Ric, through-neck and all, and generally keep it with the strings de-tensioned to avoid issues. Needless to say, it gets played very little, whereas I have no worries about keeping Fenders in tune all the time.
Questions or Inquiries?
Just want to say Hello? Sign the .