Walnut
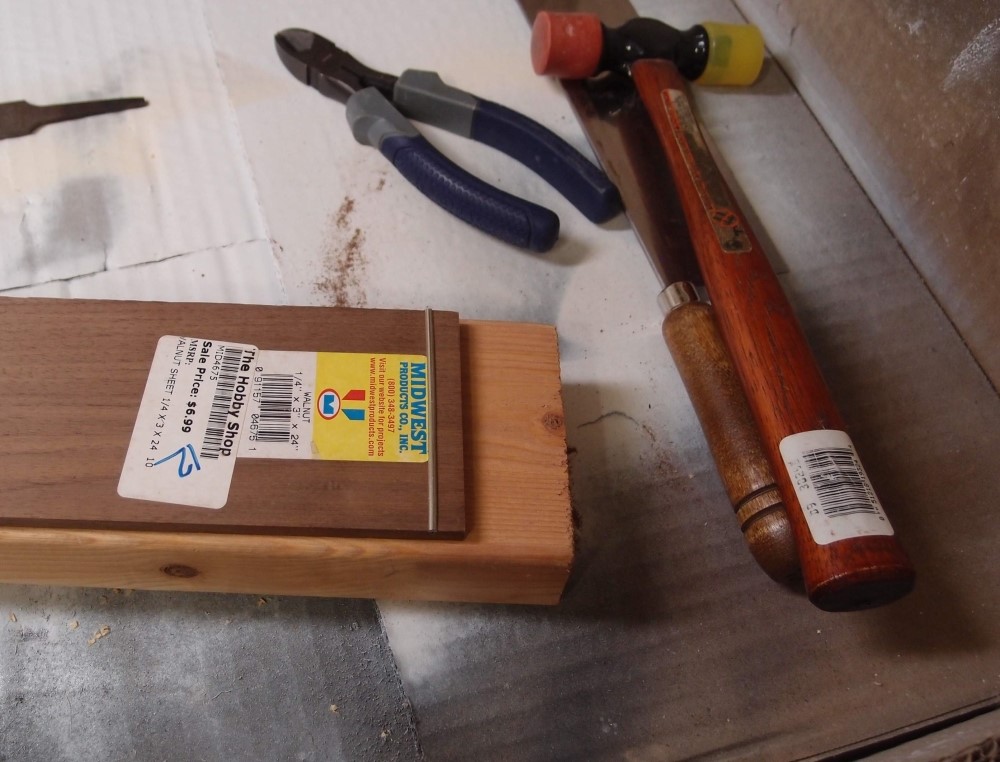
This photo speaks for itself. I got this nice piece of 1/4" walnut at the local hobby shop. They have lots more like it. Walnut is softer than hard maple - 1010 vs 1450, but otherwise similar in strength - 1.7 vs 1.8. I've read a lot on the internets about walnut fretboards, and come to the conclusion that 90% of it is BS - know-nothings stating their suppositions as facts, or repeating standard luthier nonsense.
It seems that in cases where walnut is actually used, it works fine. For comparison, the tropical hardwoods that are commonly used as fretboards have hardnesses from around 2000 to well north of 3000. But that may all just be increasing levels of overkill. There must be some threshold of hardness that makes a wood suitable for a fretboard. Maple is the softest wood that is commonly used, but Fender pioneered maple fretboards solely for cost reasons, it had nothing to do with material properties. If there has been much work done with other woods, it is poorly reported. ( As if luthiers are scientists! They're the opposite. Luthiery has more in common with alchemy than carpentry. )
So I freehand-cut a slot in the end of the board and hammered in a piece of fret wire, with no glue. The wire had a pretty strong curve to it, and the board is flat, so there should be a lot of stress there trying to pry the wire out of the wood. It is in there nice and tight now; I will let it sit and see what happens. This is the harshest test I can make - if it was a real guitar, I would do everything much better. I'll bet that piece of wire stays right where it is, until I pull it out.
One thing I would do with walnut is put a finish over it, like you would with maple. Walnut is not naturally oily like rosewood, and might suffer in the long run. Several coats of polyurethane prior to fretting, and one or two afterward, should seal it up good. In addition to walnut, the hobby shop also has cherry and mahogany, in many thicknesses. I wouldn't consider either of those for a fretboard, but any of them can be used to make a neat decorative stripe under a maple fretboard, and at the same time build up the thickness of a standard 3/4" piece of maple if needed.
Brian May used oak for the fretboard on his "Red Special" in the 1960s, and he is still playing it today. Oak has a hardness around 1300, between maple and walnut. I also have a piece of red oak from the hardware store that I plan to try someday. Oak can be blackened by soaking in a solution of white vinegar and steel wool, a stronger version of what happens when you set a cold glass on it without a coaster.
If anyone has any direct experience with this, I'd like to hear it. Not interested in what you may have read or heard somewhere, I've probably already seen it and discounted it. But if you've actually ever done something like this, or have an old instrument you could report on, then please chime in.
Questions or Inquiries?
Just want to say Hello? Sign the .