Fretboard Gluing
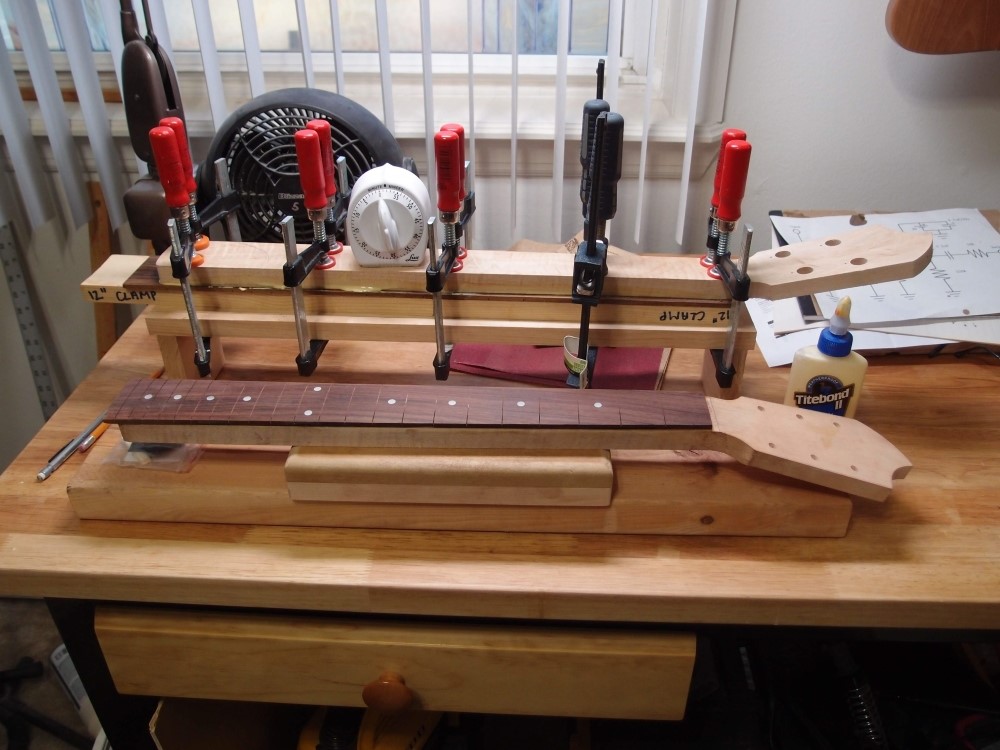
It's time to glue up some necks. First I radius-sanded the fretboards to 12 inches with my DIY sanding block. The StewMac board started with a 16" radius, which was easy to do. The other board started flat and was a lot of work to do entirely by sanding, not to mention a mess of nasty rosewood dust. For a flat board, better to rough it out with a router, and then finish by sanding. I'm not much of a cook, but the little kitchen timer has a thousand uses.
The same little jig that I glued up the angled headstocks on is perfect for gluing fretboards. I used matching 12" radius cauls that I made the same way as the sanding block, and lots of clamps, on both sides. Clamping the center is not good enough - you want to clamp the edges, and you can't use too many clamps. Finally, after the glue is set up, I radius-sanded the fretboards again, this time to get them perfectly straight. Sighting with a ruler against the light will show you the low and high spots. Scribble over the surface with a pencil, then erase the pencil marks with the sander. Eventually, you'll get it near to perfect, and the rest can be fixed with a little fret dressing.
I want to glue the fixed truss rod in tight, but not the adjustable one. A strip of cellophane tape over the truss rod slot will keep the glue out. At least, I think it will, I'd have to destroy the neck to find out for sure. Cellophane tape is about as thin as you can get, and although it may grab the rod at first, it is pretty weak stuff and will let go in time.
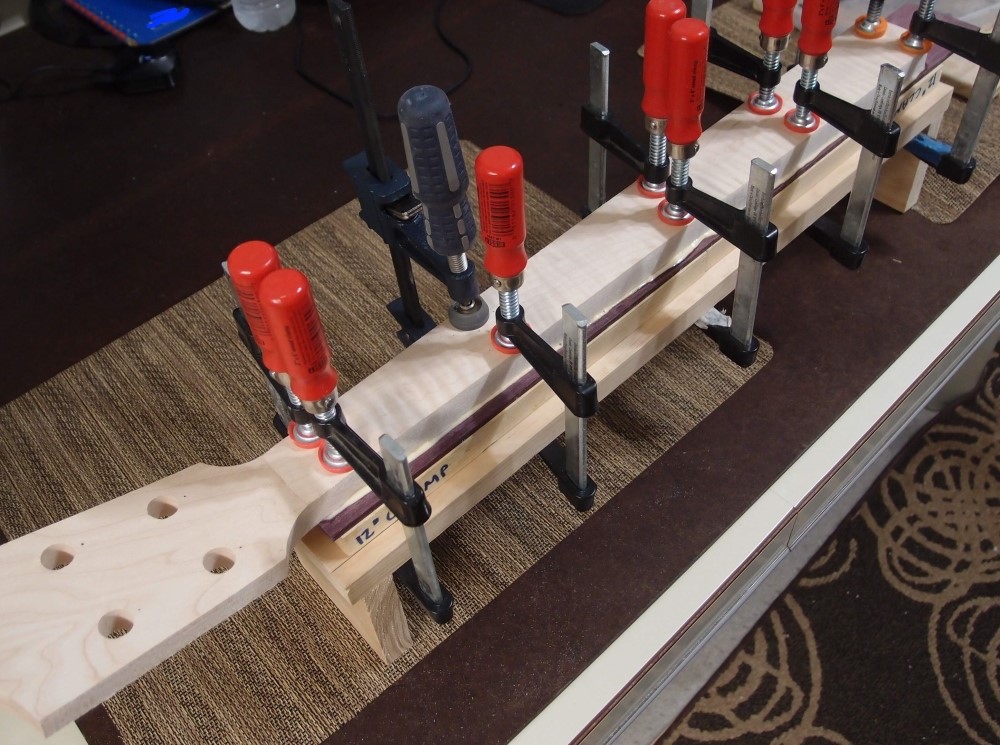
I originally made this little table-like thing out of scrap pine to glue up headstock joints, like the one in the picture. But it is good for gluing on fingerboards as well. It could be a little longer, but it is good enough. I laid the radiused clamping cauls on it, then the fingerboard face down, then the neck on top, and clamp the whole mess firmly. The neck is roughly shaped, while the fingerboard is uncut rectangular. This lets me align everything easily, simply eyeballing the neck against the fingerboard while aligning the nut end of the fingerboard against a mark on the side of the neck. This is much easier than trying to align centerline marks from the other side.
Note that the clamps are in pairs along the edges, to make sure that there is no gap when the glue is dry. You can't use too many clamps. For a job like this, I like these little screw-type clamps better than springs. Plenty of glue squeeze out all around. Nothing special about this jig, cost nothing and took 5 minutes to make, no fasteners, just glue. The point is how much better and easier you can make a job with a little forethought and the right tooling.
Questions or Inquiries?
Just want to say Hello? Sign the .